Whilst building my guitar I did not have access to many advanced tools such as one would find in a professional machine shop or woodworker's den. I really had to sit down and make some serious decisions about what I would and would not use during the build. I reasoned that, far back in the mists of time ,that guitar builders would pretty much do everything by hand but then the real horror of that struck me. I quickly realised the secret was, if I could not do it on my boat, I would get other people to do it for me who had the tools and gear! Logical really! That really was the bottom line of how I would get things done with my available space and resources. Get the timber cut as near as dammit to size before you start. had I realised this simple thing I probably would have started on building a guitar a long time ago!
I built my guitar whilst living on my boat "The Nicky J Miller" in the North of Queensland. Naturally, I had a few simple power tools but nothing more than that. I did have access to a rusty old Triton Bench saw and was able to make use of that for cutting the braces but they could have easily been done with a hand saw!
Sander Orbital
Optional desirable tools! Ones I didnt have!
Bandsaw, a planer, a router (I hate them and don't own one!)
TOOLS I USED FOR BUILDING MY GUITAR
( strangely enough, I didnt even use all of these tools either!)
· A rusty old Triton workbench (only for the braces)
· A small block plane
· A sharpening stone and some oil
· A set of chisels 6mm to 25mm
· A chisel and plane honing guide (an absolute must)
· A set of cheap saws consisting of a hand rip saw, a small keyhole saw, a retractable exacto type knife.
· A stainless steel scraper.
· Ten or twelve six inch clamps.
· Several small G clamps
· Three cam clamps
· A set of needle files
· A tenon saw
· A hobby type hacksaw
· A dovetail saw
· A coping saw
· A jeweller's tenon saw with a packet of 000 blades
· A flat smooth woodworkers file.
· Jewellers pincers small
· A small hammer
· A small jewellers vice
· A small red vice.
· A one metre straight edged engineer's rule (invaluable)
· A one foot steel rule (in inches)
· A foldaway builders steel tape (in inches and millimetres)
· Various sanding blocks (rubber and foam)
· A Bernz-o-matic plumber's gas torch with a regular nozzle
(I would recommend a larger nozzle)
· Several small assorted fine toothed saws
· Several packets of sandpaper ranging from some cheapo bargains in all grades to some really good expensive non clog stuff ranging from 80 grit to around 800grit....some wet and dry about 400 grit
· A packet of 000 fine wire wool
· A jar of orange shellac (flakes) and a litre of methylated spirits
· Several odd little clamps that were lying around the boat
· A large packet of super big elastic bands
· About twenty very large rubber bands made from an old car tyre
· A twenty-dollar cheap and cheerful folding workbench (a kit from Supercheaps!)
· A tapered reamer from Supercheaps
· A few half decent paint brushes and pots.
ELECTRIC TOOLS
I had the usual electric tools that are usually found around a house or boat. These were as follows:
· An electric drill
· A jigsaw
· A variable speed rotary sander..this is a wonderful tool and I used it for nearly all sanding jobs.. the great beauty of this machine is the variable speed, you can pull it right down to about 75 rpm and it is very gentle to use.. Normal sanders are stupid and lethal and really should be banned! What on earth is the good of a machine that kicks in from nought to twenty thousand revs in a second or two...I hate them, they are only good for cutting roof tiles or steel even then they are still lethal!!
· A six inch rotary bench saw ( never used it!)
· A Bosch variable speed electric orbital sander and a lot of discs ranging from 120grit to 400grit ....( this tool was fantastic for sanding the braces, backs and soundboard)
· A Colt or Dremel mini variable speed rotary drill and kit... I bought a few accessory kits for this machine most of which I did not even use except the rotary sandpaper drums for sanding down the braces to a point! and honestly I just could not have built this guitar without this little wonder of a machine!...sadly, it burned out on the very last stages of the build but I will buy a Dremel next time or even a Ryobi!
These machines are the last word if you need to do any inlaying, but if you do, buy this book;
"The Art Of Inlay by Larry Robinson"....it is indispensable if you are even thinking about tackling any inlaying!
One obvious thing is, of course, Keep your tools, chisels and planers sharp! I have posted another article I have written called " How to keep your tools sharp using automotive wet'n'dry paper. You will find it very useful I'm sure!
I also have bought a honing guide and it's a great little machine too and you can still use the Automotive wet'n'dry to sharpen them too!
HUMIDITY, THE SOGGY QUESTION!
I'm going to say a few words about humidity. When I first said I would make my guitar on a boat, the immediate response was
" What about the humidity?" Well, firstly in Australia where I built the guitar in summer it is horribly humid and there is no way I would have attempted it then during the Summer or 'wet' as it is known.. However, I have lived on my boat for about seven years and own eight guitars. My boat is beautifully warm and dry and I have never had a problem with any of them at all. I do, however, keep them in their cases at most times. However, in the Winter, it's a different story, There are many days when the humidity is well below sixty percent and that's fine for glueing up the guitars. It's much the same as anyone who lives in a waterside house or apartment..... what do they do? I simple listen to the marine forecast or look at the weather on the computer and they can tell me whatever the humidity was just ten minutes ago! So really, I don't have a problem with dreaded Humidity folks!
All of this information and much more can be found in Terry's book that he wrote about the build called " How to build a weissenborn lap steel guitar" This can be found on terry's site as well as photos of the build, and even a sound clip of the finished guitar! This can be found at http://www.buildaweissenborn.com
Black Friday Dynabrade 59020 Dynorbital-Spirit Non-Vacuum Random Orbital Sander, 5-Inch 2011 Deals
Nov 28, 2011 03:59:43
Click for larger image and other views
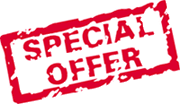
Black Friday Dynabrade 59020 Dynorbital-Spirit Non-Vacuum Random Orbital Sander, 5-Inch Feature
- Optional vacuum conversion kits are available to easily convert non-vacuum tool to self-generated vacuum tool or central vacuum tool
- Floating rotor utilizes five blades, producing more usable power. Less air is used more efficiently to maintain maximum power
- Comfort Platform provides additional hand and wrist support. Also offers increased protection against cold air exhaust
- Throttle lever recesses into housing grip when depressed, eliminating pressure-point on operator's palm
- Speed Control allows thumb-control regulating of tool speed. Lighter air-motor assembly, ideal for vertical and overhead sanding applications
Black Friday Dynabrade 59020 Dynorbital-Spirit Non-Vacuum Random Orbital Sander, 5-Inch Overview
25 hp., ergo-palm style grip, 12,000 RPM, 3/16" dia. orbit, with rear exhaust sander. Less weight only 1.4 lbs. Lower profile only 3-1/2" hig. Made in USA! Anti-clog vacuum design with a replaceable drop-in motor. New I.D. markings. Color coded composite lever (identifies orbit size), low sound levels and a one-piece speed control dial. Custom engineered composite cylinder with a double row balancer bearing that keeps out contaminants. Includes low profile premium urethane, weight-mated, non-vac pad (PN56106). Can be converted easily to self-generated or central vac model for hook-up to dust collection system.SAVE NOW on Black Friday offers below!
Available In Stock. |
This Black Friday Dynabrade 59020 Dynorbital-Spirit Non-Vacuum Random Orbital Sander, 5-Inch ships for FREE with Super Saver Shipping. |
Price : Click to Check Update Prices Please. |
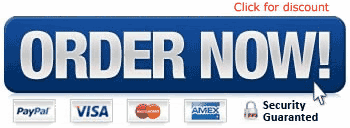